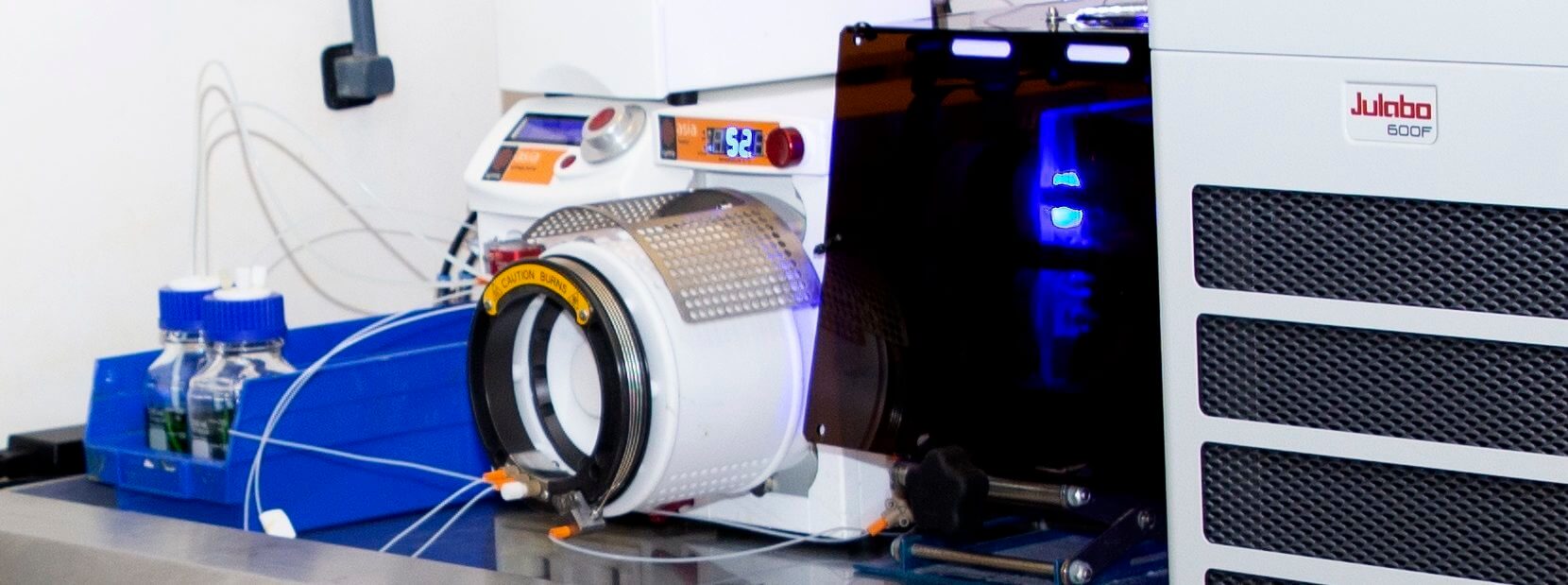
The Problem:
A large pharmaceutical company had a fascinating chemistry problem wherein they were performing a Bestmann Ohira reaction to introduce an alkyne functionality to a crucial, enantiomerically pure intermediate. Beginning with a traditional batch chemistry method, epimerization of the stereo center was observed, resulting in a product with low diastereoselectivity. Seeing all the advantages continuous flow chemistry offers (improved yields, purity, reproducibility, and a variety of others) the company developed a proof-of-concept method. The flow chemistry process provided high diastereomeric purity, but an inorganic by-product crystallized out of solution clogging the system, rendering continuous operation not feasible. The client turned to Adesis to optimize the difficult chemistry.
The Solution:
The chemical challenge could be addressed on both fronts using traditional batch process and continuous flow. Using batch process, Adesis chemists improved the yield of the reaction and retained a significant level of diastereoselectivity, but the purification of the final product remained a challenge. The answers would lie in flow chemistry.
By focusing on flow chemistry techniques to finely tune the reaction conditions, the issue of byproduct crystallization was overcome entirely. By altering the original base used in the reaction, carefully controlling the mixing and residence time of the deprotonation process, and identifying a suitable co-solvent to aid in the solubility of the material, we achieved up to 90% yield and complete diastereomeric purity retention. The reaction time was reduced from 2 hours to 10 minutes in flow, minimizing product decomposition. Using a lab scale reactor, a throughput of 1kg per day is possible, and this process has the potential for direct scalability up to 10kg per day using Adesis’ equipment.
Conditions | Yield | Diastereomeric purity |
Original Batch method: – 40 °C, 2 hours | 50% | 72% |
Optimized Flow method: -25 °C, 10 minutes | 90% | 98% |
The Outcomes:
In just three weeks Adesis’ team of flow chemistry scientists and engineers optimized the reaction and increased the yield from 50% to 90% without the troublesome epimerization issue. Product purification was simplified due to the cleaner reaction crude product. Moreover, we were able to return to the client with a purer, higher-yielding process with the potential to scale up to 10kg per day through continuous flow chemistry methodology.
This singular case study illustrates how effective continuous flow chemistry can help the pharmaceutical industry optimize chemical reactions, improve yield and purity.
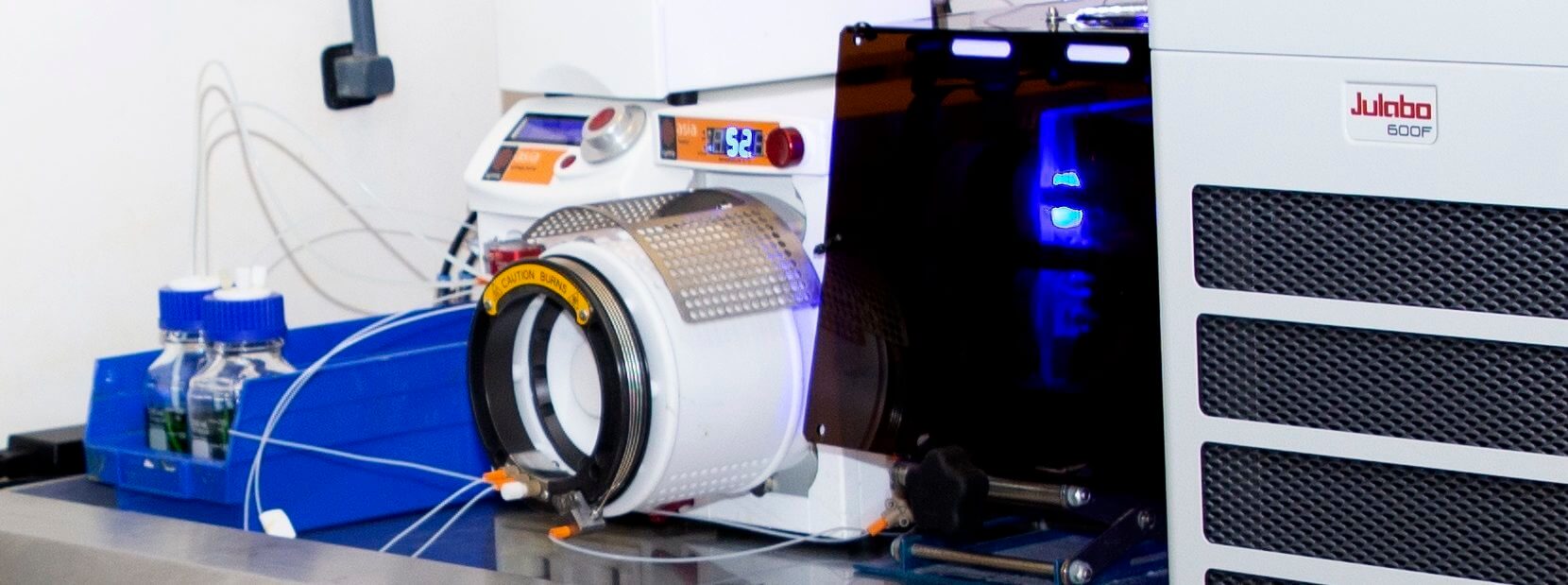
References:
Manoj Dhameja, Jyoti Pandey. Bestmann-Ohira Reagent: A Convenient and Promising Reagent in the Chemical World. Asian Journal of Organic Chemistry 2018, 7 (8), 1502-1523.